Did you know that compressed air generation amounts to over 40% of a plant’s total electricity bill? And that energy consumption can account for over 80% of a compressor’s lifecycle cost? Atlas Copco pioneered Variable Speed Drive (VSD) technology in the compressed air industry to help businesses reduce energy consumption and increase their profits. While continuing to invest in VSD, we have also developed a range of control, monitoring and energy recovery technologies that reduce running costs while protecting the environment for future generations.
Reducing consumption throughout your process
What is Variable Speed Drive (VSD)?
Atlas Copco’s VSD technology automatically adjusts the motor speed to air demand, reducing energy consumption by up to 35% and cutting the compressor’s life cycle cost by an average of 22%. In addition, lowered system pressure with VSD dramatically minimizes energy use across your production.
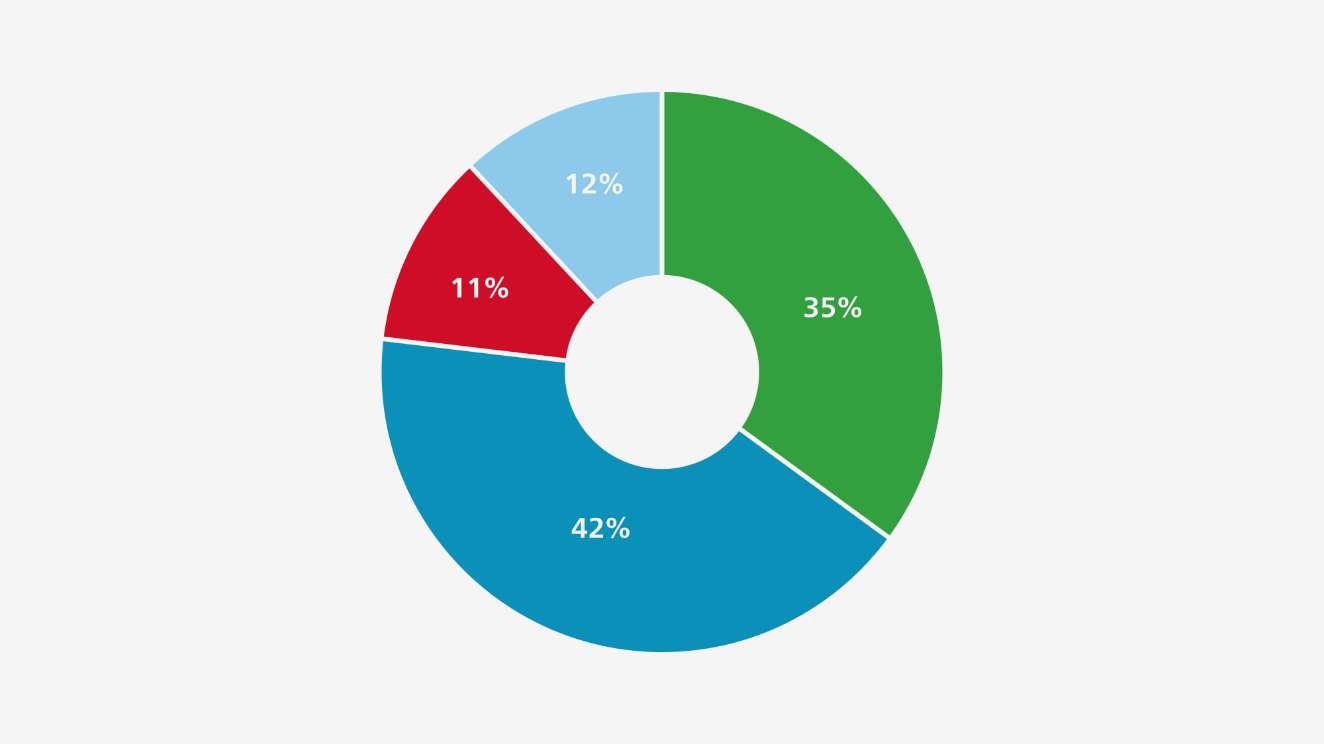
42% = Energy
35% = Energy savings with VSD
12% = Investment
11% = Maintenance
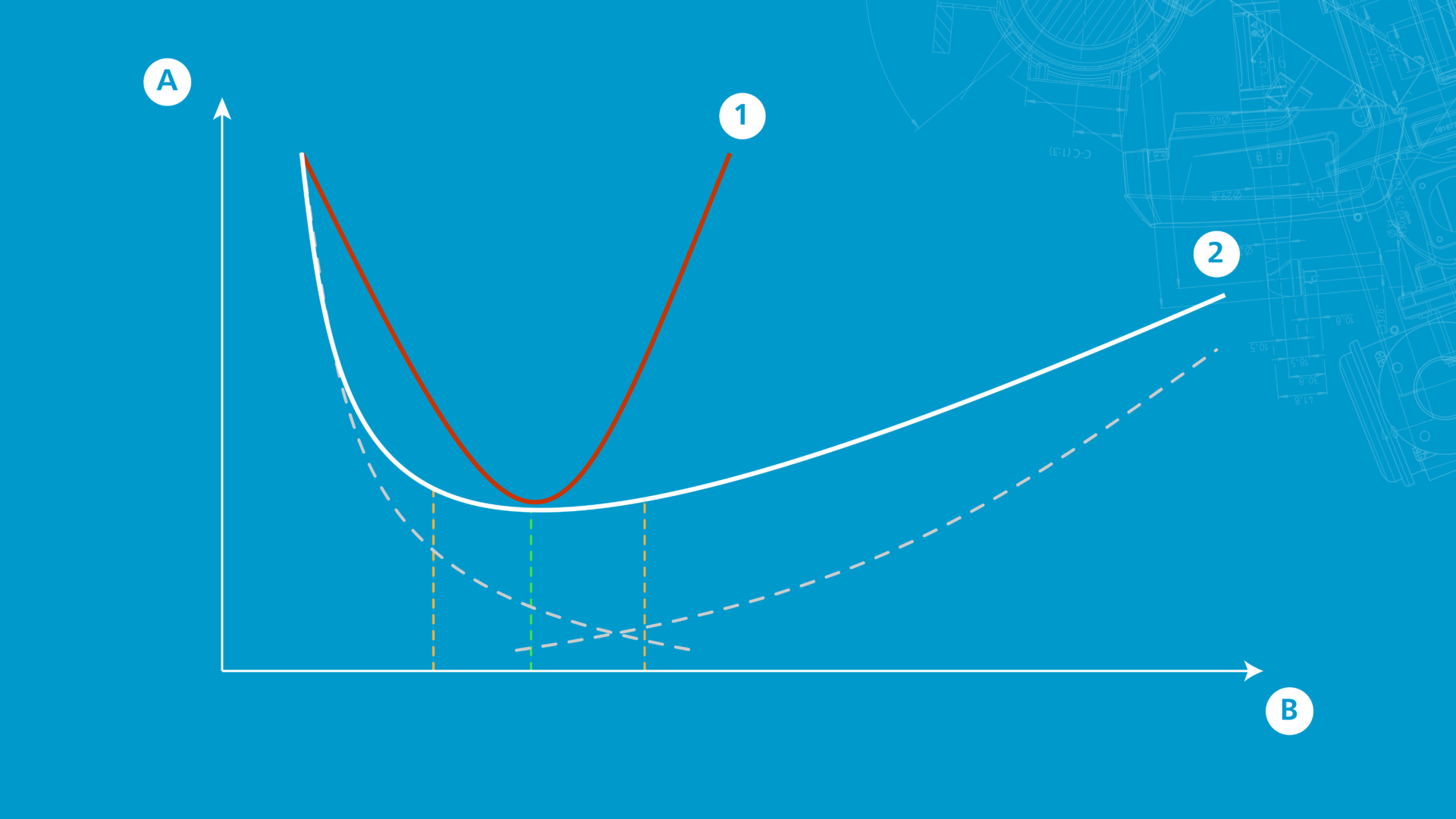
A = Losses
B = Speed
1 = Total losses traditional element
2 = Total losses Atlas Copco element
Elektronikon® with advanced control algorithms for more energy savings
Delayed Second Stop (DSS): in traditional fixed speed machines (load/unload), when a compressor reaches the unload pressure, the machine will be kept running in unload for a fixed time, to prevent too frequent starting and causing the electrical motor to overheat. Our sophisticated Delayed Second Stop (DSS) will take the running conditions of the machine into account and will allow the machine to stop if no frequent motor starts preceded. This will generate major savings compared to traditional load/unload compressors.
Timer functions: often, machines are kept running overnight and during weekends, even if there is no need for compressed air during these times. This is avoided with timer functions that stop your compressors when no air is needed.
Dual pressure band: even if compressed air is needed during nights and weekends, the required pressure is often lower in these periods. By implementing a dual pressure band with lower settings during nights and weekends, you can create considerable energy savings.
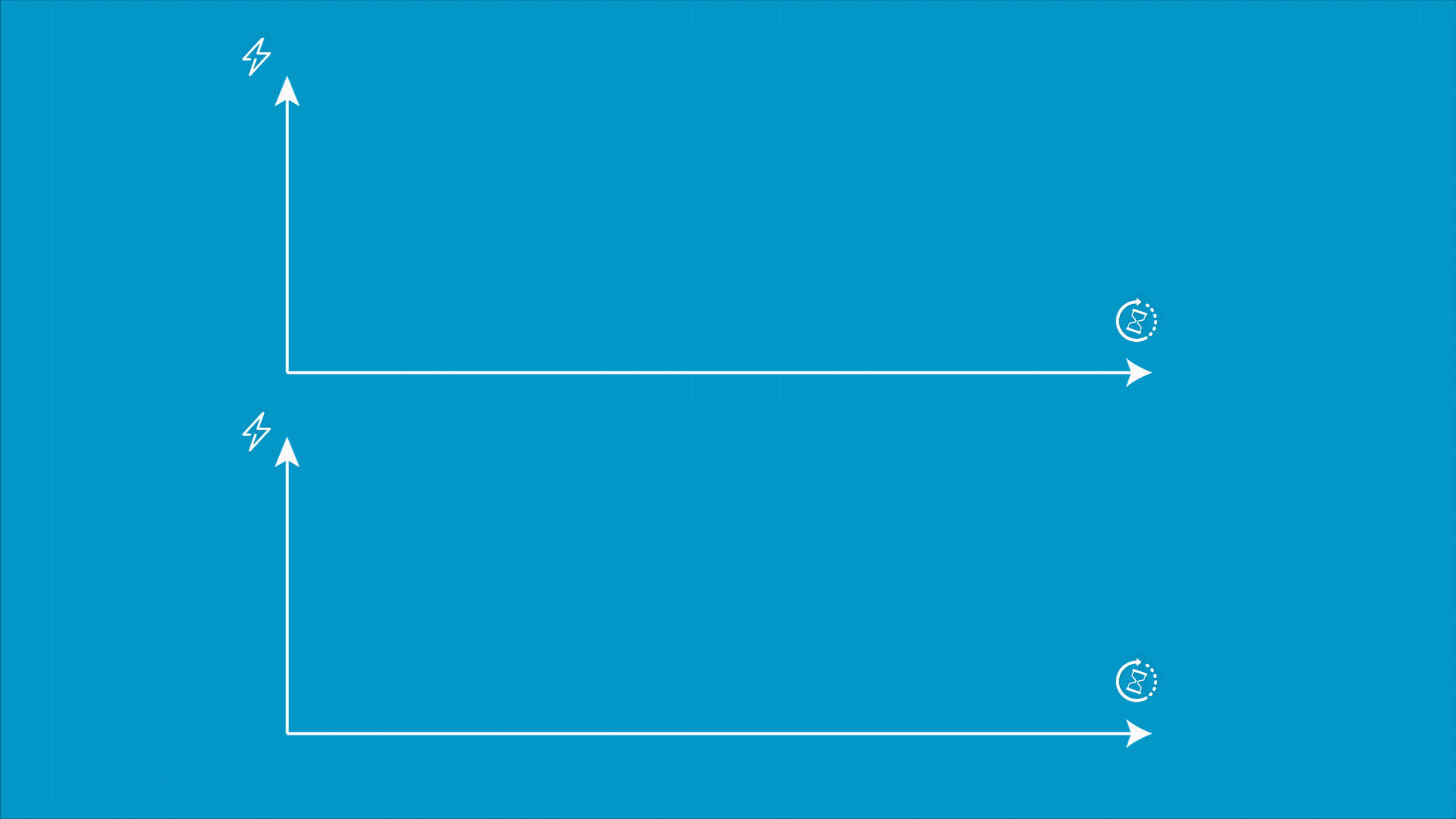
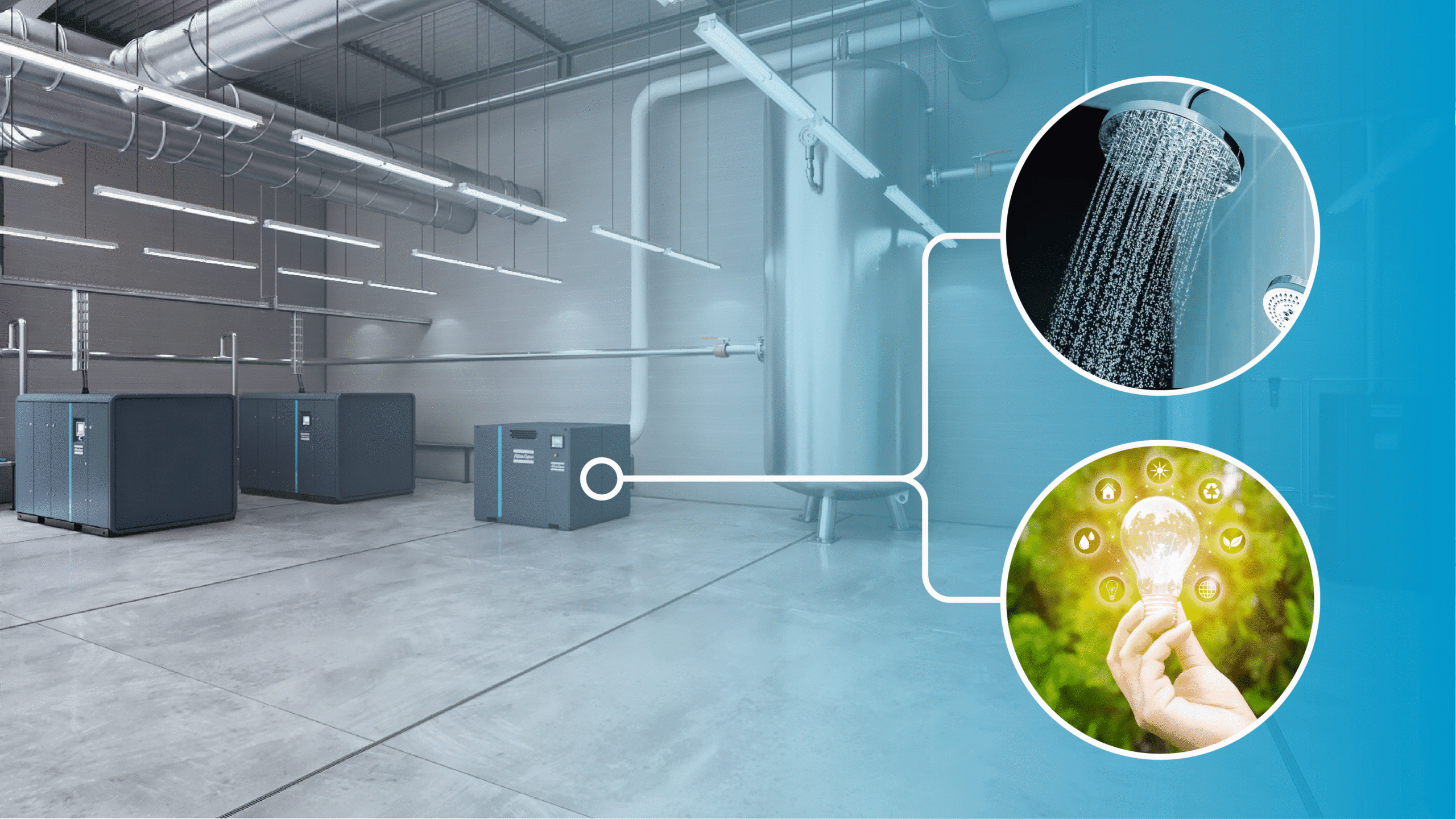
Energy Recovery: turn your compressor into an energy source
Compressed air is a vital utility for many industries. It is also one of the largest consumers of energy. Our ZR compressors equipped with Energy Recovery can help you reduce energy bills and your carbon footprint. In a typical process, up to 94% of the electrical energy is converted into compression heat, which is lost into the atmosphere via the cooling system and radiation. With Energy Recovery, you can recuperate this energy as hot water for sanitary purposes, space heating or, even more effectively, process applications. By using the hot water as boiler pre-feed or directly in processes requiring temperatures of 70 to 90°C, you will reduce your consumption of more costly, carbon-based energy sources such as natural gas and heating oil.
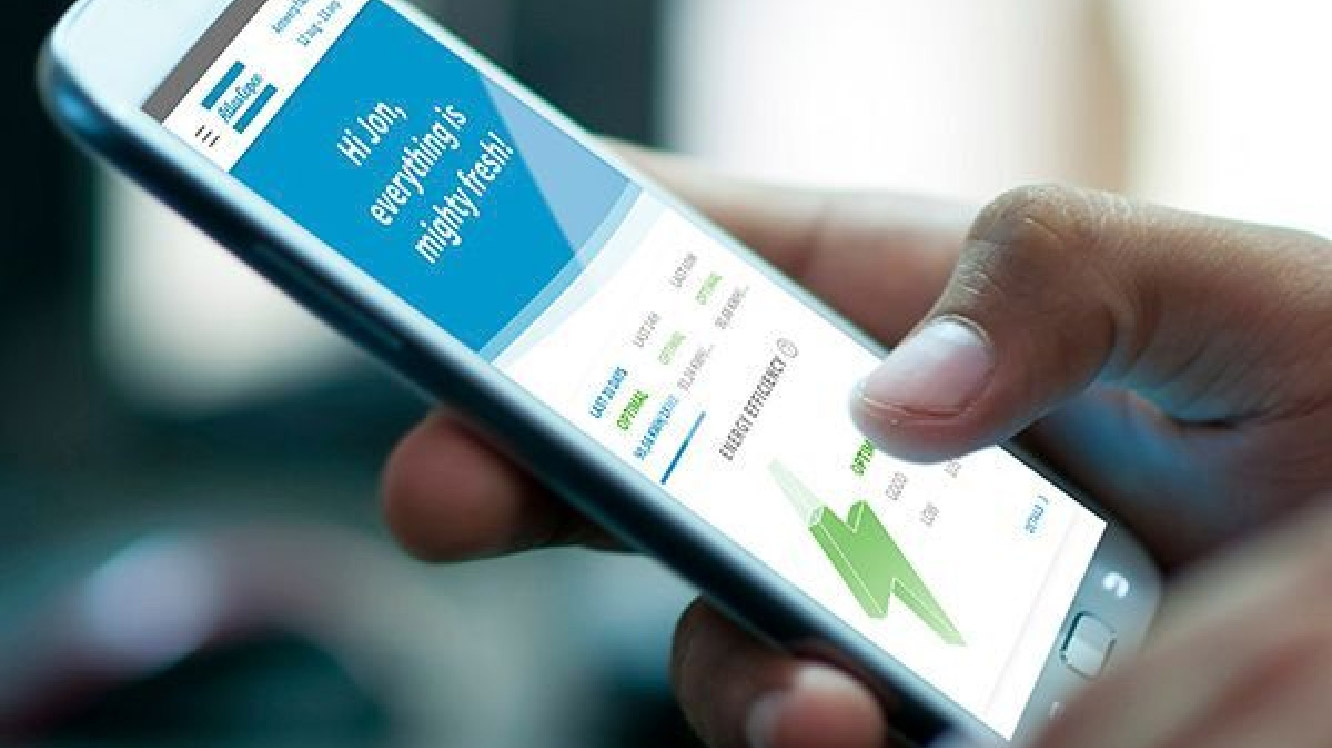
SMARTLINK for expert monitoring
Knowing the status of your compressed air equipment at all times is the key to efficiency and availability. SMARTLINK provides customized reports on your compressor room’s energy performance as well as early warnings, and timely component replacement alerts to increase uptime and prevent production loss.
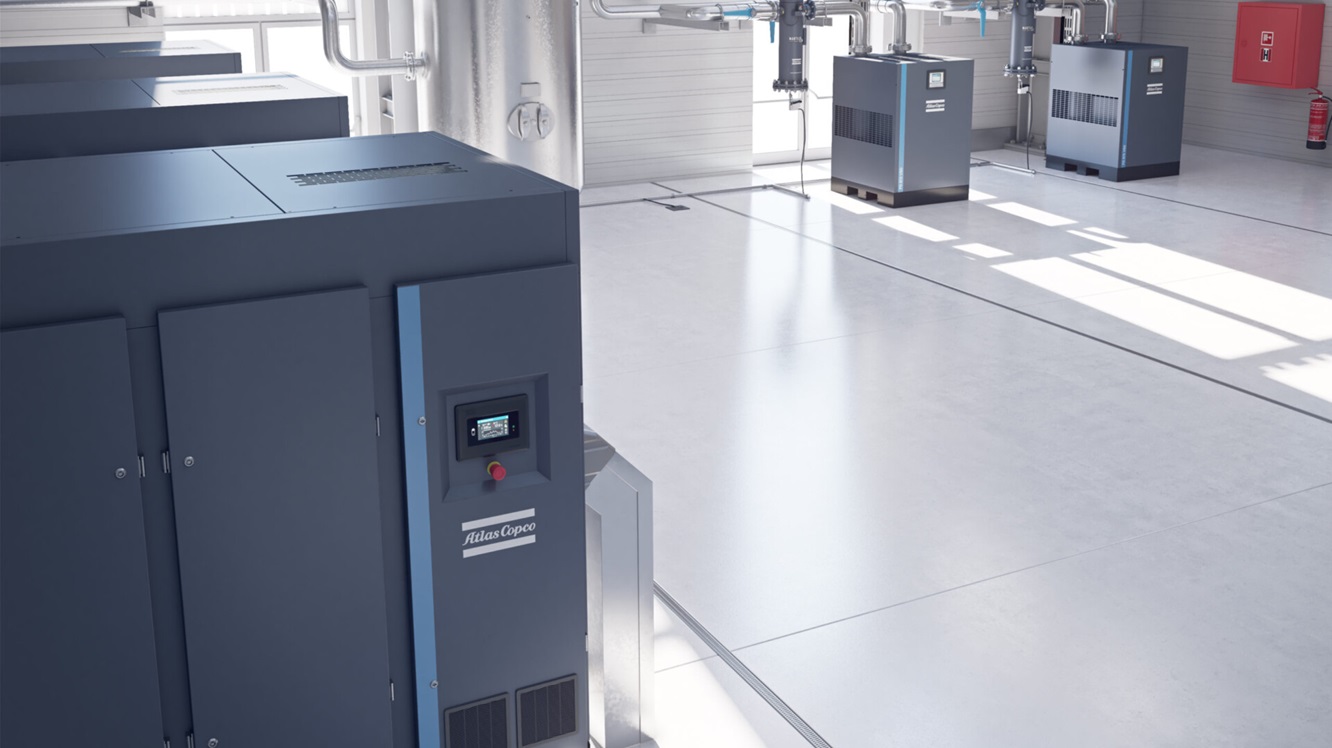
Dual set-point and automatic stop
Most production processes create fluctuating levels of demand which can lead to energy waste in low use periods. Using the Elektronikon® unit controller, you can switch manually or automatically between two different setpoints to optimize energy use and reduce costs at low use times. In addition, the sophisticated algorithm runs the drive motor only when needed. As the desired setpoint is maintained while the drive motor’s run time is minimized, energy consumption is kept to a minimum.
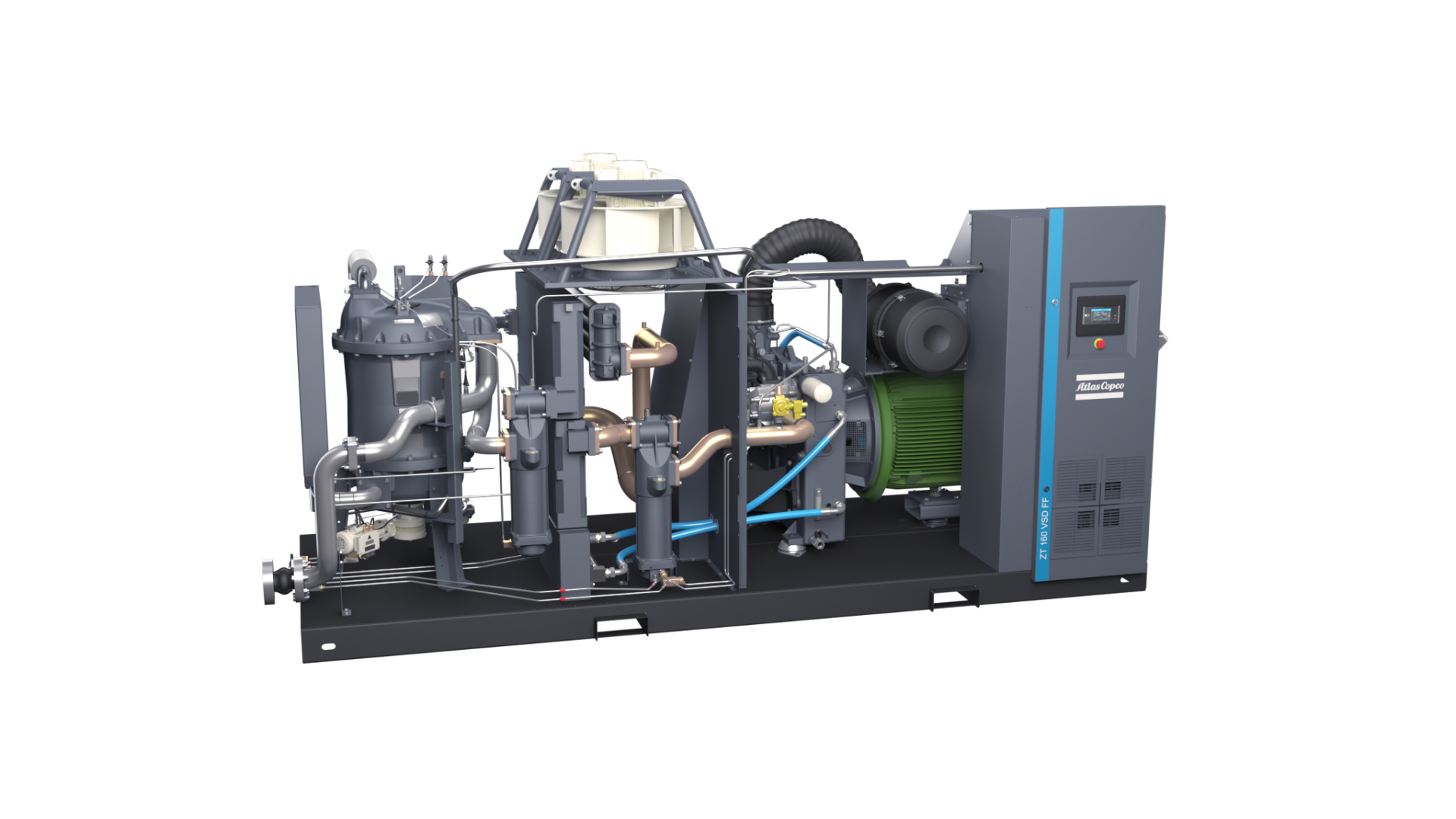
Components designed for efficiency
Our engineers took every opportunity to reduce energy consumption in the ZT and ZR compressors. The element has a superior coating for increased efficiency. High-performing intake filtration ensures minimum losses and low pressure drop. The coolers are also designed for efficient operation with low air approach temperature and low pressure drop. The water separator efficiently separates the condensate from the compressed air.